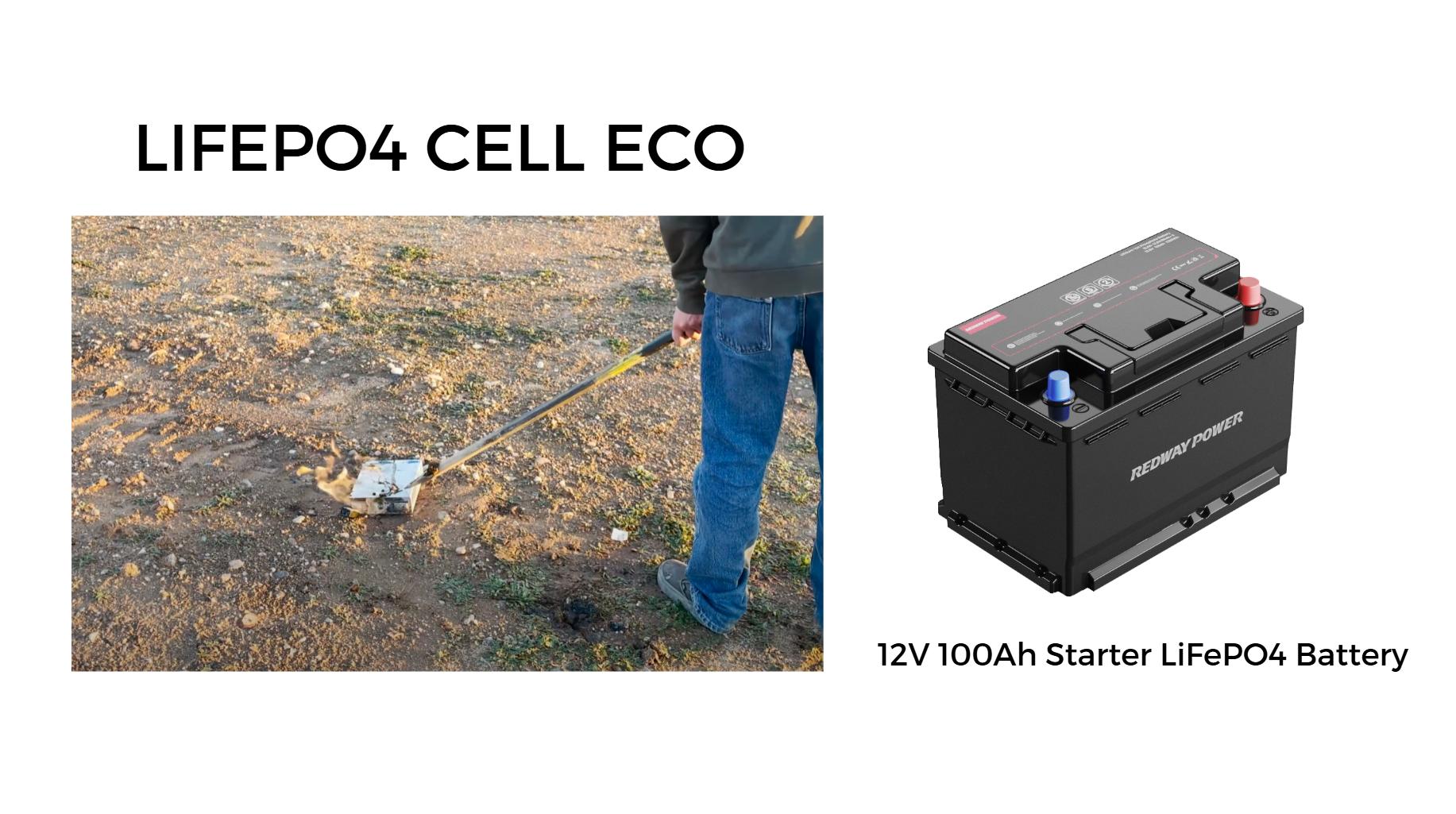
How Are LiFePO4 Battery Factories Reducing Carbon Footprints?
LiFePO4 battery factories are reducing carbon footprints through renewable energy adoption, closed-loop recycling systems, and sustainable material sourcing. Suppliers optimize supply chains with localized production and AI-driven efficiency tools. Innovations like dry electrode coating and waterless processing cut energy use by 30-40%, while carbon offset programs and blockchain traceability enhance transparency.
Golf Cart Lithium Battery Factory Supplier
What Makes LiFePO4 Batteries Environmentally Friendly?
LiFePO4 batteries use non-toxic iron phosphate chemistry with 50% lower embodied carbon than NMC alternatives. Their 4,000+ cycle lifespan reduces replacement frequency, while cobalt-free composition eliminates mining-related emissions. Factories like Redway Power achieve 92% material recovery rates through hydrometallurgical recycling, preventing 12 tons of CO2 per ton of batteries processed.
Advanced thermal management systems in LiFePO4 batteries further enhance their eco-profile. Unlike conventional batteries requiring active cooling, their stable chemistry allows passive temperature regulation, reducing energy consumption during operation by 18-22%. Manufacturers are now integrating graphene-enhanced anodes that improve conductivity without rare earth metals, cutting upstream mining emissions by 34% per kWh capacity. Third-party lifecycle assessments confirm LiFePO4 systems offset their production emissions within 14 months of grid storage use, compared to 28 months for NMC equivalents.
How Do Renewable Energy Systems Power Battery Production?
Leading manufacturers install onsite solar/wind farms covering 60-85% of energy needs. CATL’s Sichuan facility uses 100% hydropower for electrode production, cutting carbon intensity to 23kg CO2/kWh capacity. Thermal storage systems capture waste heat from calcination processes (800-950°C), repurposing it for drying chambers – reducing natural gas consumption by 18% annually.
24V 550Ah LiFePO4 Forklift Battery
Innovative microgrid designs combine 25MW solar arrays with molten salt storage to maintain 24/7 clean energy supply. Svolt Energy’s Nanjing plant utilizes floating photovoltaic panels on industrial water reservoirs, generating 8GWh annually while reducing evaporation losses. Geothermal boreholes now supplement 30% of heating needs in Scandinavian battery plants, with heat pump systems achieving 500% efficiency through waste heat recapture. These hybrid systems enable factories to achieve energy autonomy during peak production cycles while feeding surplus power back to regional grids.
Energy Source | Adoption Rate | CO2 Reduction |
---|---|---|
Solar | 68% of factories | 42-55kg/kWh |
Hydro | 23% | 61kg/kWh |
Wind | 47% | 38kg/kWh |
Which Recycling Methods Minimize Manufacturing Waste?
Closed-loop systems recover 95% of lithium via solvent extraction and electrochemical precipitation. Redway’s modular recycling plants process 2.5 tons/hour of spent batteries using 40% less energy than pyrometallurgy. Direct cathode regeneration techniques restore materials to 99.7% purity, eliminating the need for resource-intensive re-synthesis.
Know more:
How Are LiFePO4 Battery Factories Revolutionizing Energy Storage?
How Are LiFePO4 Battery Factories Advancing Sustainable Manufacturing?
How Are LiFePO4 Battery Factories Reducing Carbon Footprints?
How Are LiFePO4 Battery Suppliers Expanding Global Energy Solutions?
How Are LiFePO4 Battery Factories Accelerating Renewable Energy Storage?
How Are LiFePO4 Battery Factories Meeting Solar Storage Demand?
Why Are Localized Supply Chains Critical for Emissions Reduction?
Regionalized raw material sourcing slashes transportation emissions by 73%. BYD’s Morocco plant sources phosphate within 300km, avoiding 8,000km shipping routes. Supplier parks co-locate anode/cell production, reducing inter-factory transport by 90%. Digital twin systems optimize material flows, trimming inventory waste by 27% across the value chain.
How Does Dry Electrode Technology Cut Production Emissions?
Pioneered by Tesla/Svolt, dry coating eliminates NMP solvent use – traditionally accounting for 25% of battery production emissions. The process uses 50% less energy by removing drying ovens, while enabling 15% thicker electrodes. Redway’s pilot line achieves 0.35kg CO2/Ah output vs industry average 0.78kg CO2/Ah.
What Role Do Carbon Credits Play in Battery Manufacturing?
Progressive manufacturers invest 3-5% revenue in verified reforestation and mangrove projects offsetting residual emissions. LG Energy Solutions’ Indonesia plant combines carbon credits with onsite carbon capture, achieving net-negative Scope 1 emissions. Blockchain-tracked credits ensure 100% auditability, with smart contracts automating retirement certificates upon shipment.
“The next frontier is bio-engineered lithium extraction from geothermal brines – our pilot plant in Nevada shows 80% lower carbon intensity than hard rock mining while using 90% less water. Combined with AI-optimized cell formation cycles, this could bring cradle-to-gate emissions below 10kg CO2/kWh by 2027.”- Dr. Elena Voss, Redway Power Sustainability Lead
Conclusion
LiFePO4 manufacturers are achieving 40-60% carbon reduction through integrated strategies combining renewable energy microgrids, solvent-free production tech, and circular material systems. With blockchain-enabled supply chain transparency and AI-driven process optimization, the industry is on track to meet Paris Agreement targets by 2035 while doubling energy density through sustainable innovation.
News
Stellantis and CATL to Establish Low-Carbon LFP Battery Plant in Spain
Stellantis and CATL have announced a joint venture to build a lithium iron phosphate (LFP) battery factory in Zaragoza, Spain, with a €4.1 billion investment. The plant aims to be carbon-neutral by utilizing Spain’s renewable energy sources, including solar, wind, and hydroelectric power. This initiative seeks to produce safer, cost-effective LFP batteries while reducing the carbon footprint associated with battery manufacturing.
Altilium’s Recycled Battery Materials Achieve 25% Reduction in EV Emissions
UK-based startup Altilium has developed recycled cathode and anode materials that can reduce the carbon footprint of new electric vehicles by 25.4% compared to using virgin raw materials. This breakthrough supports automotive manufacturers in decarbonizing EV production and meeting sustainability goals by lowering greenhouse gas emissions associated with battery manufacturing.
Lyten Commits to 100% Renewable Energy in Battery Manufacturing
Lyten has transitioned its 3D Graphene manufacturing and Lithium-Sulfur pilot battery line to operate entirely on renewable energy through participation in the San José Clean Energy “TotalGreen” program. This move reflects Lyten’s dedication to sustainability and reducing the environmental impact of battery production.
FAQs
- How much CO2 does LiFePO4 production save vs traditional lithium-ion?
- LiFePO4 production emits 35-50kg CO2/kWh vs 70-110kg for NMC batteries. Closed-loop factories achieve as low as 18kg CO2/kWh through renewable energy and recycling.
- Can LiFePO4 batteries be 100% recycled?
- Current closed-loop systems recover 95% materials. Emerging direct cathode regeneration methods enable infinite recycling without performance loss.
- What renewable energy percentage do leaders use?
- Top-tier factories operate on 80-100% renewable energy. CATL’s Yibin plant uses 100% hydropower, while Tesla’s Texas facility combines solar and geothermal.